产品介绍 / A.MANNESMANN 顶级螺杆 镗床主轴 / AMBS 顶级螺杆
AMBS 顶级螺杆
AMBS 渗氮硬化滚珠螺杆
由顶尖技术制造商 A.MANNESMANN 所生产
AMBS 螺杆电子型录AM 冷却系统电子型录
AM 感测系统电子型录
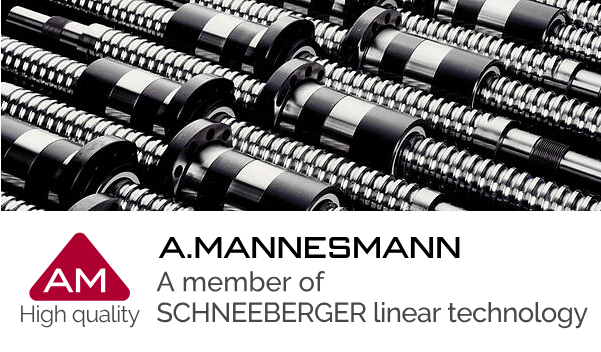
顶尖性能的精密滚珠丝杆
精密滚珠丝杆需在螺帽、滚珠与丝杆轴之间完美配合。各部件在严格公差范围内研磨后,经由技术熟练的专家手工组装,达到最高的精度水平。
所有组件均采用最高质量的材料制造。所有滚珠丝杆的表面经长期耐磨的渗氮处理,螺帽与滚珠则经整体淬硬处理,搭配优化的滚珠循环系统及高效的防尘密封装置,确保其在长期使用中的高负载能力与高精度。
在组装过程中,双螺帽在两点接触预压下达到高度的螺帽刚性,同时保持极低的内部摩擦。这也体现于系统的高效能及低空载扭矩与启动扭矩中。
平稳的扭矩曲线、高度顺畅的运行以及最小的振动倾向贯穿整个螺纹长度,减少了功率损耗并降低了热量产生,不论滚珠丝杆使用油或润滑脂进行润滑,都能达到最佳效果。
精密滚珠丝杆的安装方式及负载方向通常不受限制,不会影响其功能性。
精密滚珠丝杆的设计及连接尺寸符合 DIN ISO 3408 或 DIN 69051 标准,也可依照客户的个别需求进行特殊设计。
AMBS 特别适用于:
- 高速应用
- 超高定位精度
- 高动态
- 超长效寿命
最大性能与长期使用寿命
- 特性值可达 n × d = 200,000 以上
- 速度可超过 150 米/分钟
- 加速度可超过 20 m/s²
- 直径范围:25 至 160 毫米
- 螺杆长度可达 10 米(无分段),超过 10 米则进行耦合
- 可依需求提供客制化特殊设计
- 经深渗氮处理的精密研磨螺杆,表面硬度约为 67 HRC,确保卓越的精度与耐磨性,提供长期稳定性
- 出色的运行品质:高轴向刚性、极低扭矩及最小扭矩波动;滚珠循环系统展现经证实的运动性能,并将摩擦及热量产生降至最低
- 卓越的成本效益:凭借长寿命、长期精度及最小化的生命周期成本,提升经济效益
- 从一开始即提供专业支持:针对您的特殊应用及具体需求,提供客制化设计及技术建议
- 标准设计:符合 DIN 标准的双螺帽预压设计
- 特殊解决方案:根据您的需求,与您紧密合作,为您的特殊应用开发专属方案
A.MANNESMANN 精密滚珠螺杆的特色
- 螺帽、滚珠与螺杆的完美配合
- 螺帽与螺杆经精密研磨,符合 IT 1、IT 3、IT 5 公差等级
- 高精度分级滚珠
- 优化的滚珠循环系统
- 高效的防尘密封系统
- 螺帽、滚珠及螺杆皆使用高质量材料
- 整个主轴表面耐磨(滚珠轨道及螺杆轴端)
- 长期渗氮处理
- 坚韧且具弹性的螺杆核心
- 螺帽经整体淬硬(100Cr6 材料)
- 极高的表面硬度(67 HRC)
- 螺帽具备高几何精度
- 高负载能力
- 长期耐用性
- 双螺帽设计,带预压(两点接触)
- 可调式预压
- 具预压锁键
- 高螺帽刚性
- 低摩擦
- 低功率损耗
- 低热量产生
- 低空载扭矩
- 低摩擦扭矩
- 低启动扭矩
- 稳定的扭矩曲线
- 高度顺畅的运行
- 低振动产生
- 适用于油及润滑脂
- 手工组装滚珠螺杆
- 高质量保证
- 符合 DIN ISO 3408 或 DIN 69051 标准
螺帽 - 功能的保证者
滚珠螺帽是滚珠丝杆组件中最复杂的组件。滚珠丝杆的正常运行主要取决于螺帽的质量,因为螺帽内含滚珠轴承、滚珠循环装置及防尘密封件。预压可根据需要通过螺帽来实现,一方面避免背隙,另一方面提升刚性。对螺帽材料和设计的最高要求
由于滚珠螺帽不仅承载滚珠在滚道中的运动,还承担滚珠循环时的负载,因此与丝杆不同,螺帽始终处于持续负载中。螺帽表面的运行温度通常比丝杆表面高约 5K。为确保螺帽能在其整个使用寿命内承受高负载,螺帽通常使用高质量的轴承钢(100Cr6)制成,并经过整体淬硬处理。由于行程长度的不同,丝杆通常需要定制,但螺帽则可在一定程度上标准化。这些标准化尺寸可依据 DIN ISO 3408 或 DIN 69051 标准,或根据制造商的规范进行。然而,某些符合这些标准的螺帽在许多应用中仍属于定制的特殊组件。
不同螺帽设计的需求
尽管努力标准化,但根据需求和安装环境的不同,螺帽设计也有所不同。滚珠丝杆螺帽的首要区别在于螺帽本体的部分数量,可分为单螺帽与双螺帽。然而,由于技术制造的需要,一个螺帽系统可能包含超过两部分的螺帽。双螺帽或双螺帽及三螺帽
双螺帽是传统的螺帽设计,在机床设计中特别受欢迎,因为预压系统几乎都是两点接触系统。双螺帽的两部分装配时,滚珠被夹在主轴和螺帽的滚道之间。轴向位移可通过研磨的中间垫片或旋转螺帽部件来调整。在这两种情况下,都可增加或减少两部分螺帽的负载转数距离。双螺帽是滚珠丝杆的经典设计,一般由两部分组成,其中一部分(承载滚珠螺帽)吸收外部负载,另一部分(预压螺帽)产生预压。承载螺帽始终是将轴向力导入直接分配的螺帽部分。
根据力的分配方式,双螺帽可实现 O 型或 X 型预压。出于技术制造的原因,双螺帽的螺帽部分可设计为两部分,从而可能实现三重或四重螺帽设计。
双螺帽可设计为圆柱形螺帽或法兰螺帽。对于圆柱形螺帽,两部分螺帽在几何上完全相同,预压则通过外部垫片以 X 型预压的形式施加。
对于法兰螺帽,区分带法兰的部件与无法兰的锁螺帽。此时,预压始终透过内部的 O 型预压产生,方式为调整负载转数的轴向位移。此位移既可以透过中间环来实现,也可以通过螺帽部件的扭转来完成。
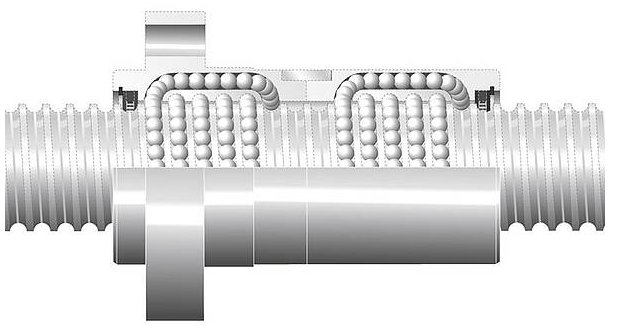
单螺帽
单螺帽是最紧凑且成本最低的螺帽设计,因此应用广泛。其结构仅包含一个带有连续滚珠轨道的螺帽本体。在最简单的设计中,单螺帽具有轻微的轴向间隙。也可通过调整负载转数和/或选择不同尺寸的滚珠及结构设计,实现无背隙的预压单螺帽。然而,由于这些设计的运行特性不完美,预压通常会导致摩擦增加、运行温度上升及磨损加剧。带预压的单螺帽对生产公差更敏感,因此非常长的主轴通常不使用预压单螺帽。不带预压的单螺帽则不受此限制,因为它们在轴向负载下始终以两点接触运行。对于具有四点接触的单螺帽,在负载峰值时不会出现滚珠卸压,因此滚珠不会滑动,因为负载传递与预压皆由相同的滚珠承担。
通过选择滚珠实现预压
消除单螺帽间隙的最简单方法是选择合适的滚珠。这些滚珠的尺寸大于螺帽与丝杆之间的间隙,该间隙由主轴及螺帽上的四个滚道边缘决定。滚珠需被强制放入间隙中,因为弹性压扁作用在滚珠和滚道上,形成四点接触。由于 DIN ISO 3408 标准不适用于四点接触的计算,因此预压大小需透过实验确定。透过滚珠选择的预压不可调整,其大小取决于滚珠的超额尺寸,并要求精确达到规定的螺纹设计。此外,在组装过程中,必须达到结构上指定的滚珠支撑点位置,才能在单螺帽中检测并维持预压力。
通过螺距偏移实现预压
对于双回路或多回路滚珠螺帽,亦可通过螺距偏移在单螺帽中实现预压。由于螺距的偏移,每个回路中的滚珠在主轴螺纹的不同边缘上独立运行。预压由滚珠在两边形成的两点接触产生。预压大小由制造的螺距偏移量决定,并可通过额外的滚珠选择进行微调。通过螺纹位移实现预压
螺纹位移也可用于螺帽中,以实现单回路滚珠丝杆的预压。在此过程中,中间的负载回路以逐步增加的导程位移制造,滚珠在一个边缘上运行,中间有间隙,随后切换到对应的另一边。预压由两边的滚珠在两点接触下产生,其大小由制造的位移量决定。预压的微调同样可通过滚珠选择完成。通过开槽螺帽实现预压
另一种实现无背隙单螺帽的方法是对螺帽本体进行轴向开槽及扭转。螺帽本体上的槽宽可透过夹紧螺钉调整,从而缩小滚珠轨道直径,并在与滚珠选择结合时形成四点接触的预压。然而,这种方法不仅会改变滚珠轨道的几何形状,也会影响螺帽螺纹的圆度,因此每个滚珠的预压和运行特性可能无法保持一致和稳定。不同的螺帽设计
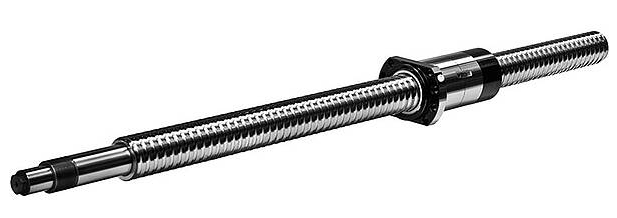
第二种区分标准:螺帽的外轮廓或固定方式
除了圆柱形设计外,法兰设计也是重要的螺帽类型。对于预压圆柱形设计的双螺帽,两个螺帽本体部分必须安装在外壳内。预压由外向内通过压力法兰产生,并透过螺帽之间的垫片限制预压量。在此情况下,预压总是以 X 型预压 的形式存在。
在法兰设计中(侧法兰或中法兰),法兰始终是螺帽本体的固定组件。预压透过两个螺帽部件相互扭转或可调的中间垫片,从内向外产生。锁螺帽仅透过滚珠和施加的预压力固定于滚道内。
可调的预压力是一项独立的组装工序,能针对应用需求进行精确调整,为高负载能力及长期耐用性创造最佳条件。
螺杆 - 承载组件
螺杆是滚珠螺杆组件中的一部分,用于承载螺帽。它是一根圆柱形轴,一般由至少两个部分组成。其中一部分包含螺旋滚珠轨道,实现滚珠丝杆全长的运动运动学。螺纹仅在当前滚珠接触区域内按顺序(部分、暂时)承载负载。支撑轴承及驱动连接部分位于另一部分,滚珠丝杆中的力和扭矩被引入或释放至机械环境中。螺杆长度和结构设计的影响
螺杆的螺纹长度通常由应用的有效行程、螺帽总长度(包括防尘密封系统和其他配件)及螺纹结束位置决定。根据长度和设计不同,滚珠丝杆可单端或双端安装,因此螺杆的整体长度可能大大超过螺纹的长度。螺杆的总长度及结构轴承设计对稳定性、旋转稳定性以及滚珠丝杆的速度和负载应用能力至关重要。A.MANNESMANN 的滚珠丝杆在严格公差范围内(IT 1、IT 3、IT 5)进行精密研磨,采用高强度渗氮钢制成,整根滚珠丝杆经过深度渗氮处理。螺杆核心坚韧,表面硬度约为 900 HV(= 67 HRC),硬化深度至少为 0.4 毫米。此极高的表面硬度是高负载能力和长寿命的基础。
结构设计的确定
螺杆设计的结构确定通常由滚珠丝杆的使用者完成,这取决于其任务和机械环境。因此,A.MANNESMANN 作为滚珠丝杆制造商的影响主要集中在优化功能和制造可能性,以及确保满足用户所需的质量。滚珠丝杆的特征包括螺纹直径、螺距、螺距方向、滚珠尺寸、螺纹长度、精度等级,以及螺纹形状和滚珠丝杆的回路数。支撑轴承和驱动连接的尺寸设计取决于轴承类型的常规尺寸及其安装需求,或驱动组件的轴-轮毂连接。
由于设计的个性化,螺杆的标准化几乎不可能实现。
不同的螺杆设计
结构设计和几何实施导致一些基本的螺杆版本,这些版本在技术上和经济上存在很大差异。有些区别可能非常显著,但并不总是直接显现出来。无论滚珠丝杆是设计为驱动型还是非旋转型,某些功能性或制造原因可能需要特殊设计,而这些设计与「普通」实心螺杆不同,包括:
- 中空螺杆
- 带法兰的螺杆
- 耦合螺杆
- 耐腐蚀螺杆
实心螺杆
大多数滚珠丝杆为实心螺杆。其横截面为实心(无孔),可在整个截面内传递对应的拉力、压力和扭矩。由于所需的加工工作量最小,实心螺杆不仅在制造技术上最简单,也是最具成本效益的设计选择。

中空螺杆
如果滚珠丝杆需要中央孔,如用于冷却或润滑,或需要在此空间中安装其他功能性组件,则可将滚珠丝杆设计为中空螺杆。在此情况下,螺杆的截面形状与具有对应壁厚的管子类似。然而,管壁的设计必须至少能确保在考虑螺纹槽深度的情况下,能够无变形且安全地传递轴向负载和扭矩。中空螺杆的优势
使用中空螺杆具有多种技术优势。例如,透过在螺杆中开孔,中空设计可进一步提高临界弯曲速度。有趣的是,在其他螺杆尺寸保持不变的情况下,随着内径的增加,临界弯曲速度会不断提升。理论上,临界弯曲速度没有不再提升的饱和点。然而,精确生产这类中空螺杆具有挑战性。中空螺杆的低质量转动惯量也是其优势之一。若使用固定-固定轴承,可透过中空螺杆的孔道输送冷却液,在加工过程中保持螺杆温度的稳定性。如此可减少所需的拉伸力,并因减少热膨胀而降低螺杆的螺距误差。
若螺杆本体采用固定-固定轴承而非传统的固定-自由轴承,且同时为中空设计,则中空设计所造成的轴向刚性损失将可藉由固定-固定轴承补偿。
与实心螺杆相比,中空螺杆质量较轻、刚性较低,但其质量转动惯量仅略微降低。
由于中空螺杆的内轮廓通常在热处理前就已成形,因此其内部也相应地具备硬度(经渗氮处理)。然而,由于质量较低,中空螺杆在生产过程中受温度影响的几何变化更大,这导致直径增加,特别是螺杆的延伸,可能影响到螺纹的螺距。由于加工难度较高,中空螺杆通常比实心螺杆制造成本更高。
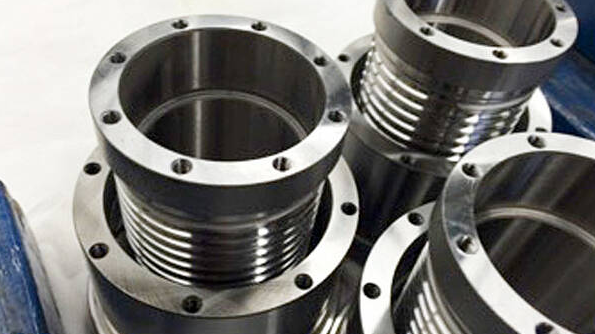
带有法兰的螺杆
滚珠丝杆的外径通常是所有其他轴尺寸的基础。在某些情况下,可能需要在特定的螺杆区域使用比滚珠丝杆外径更大的直径。例如,这可能是为了提供更大的接触肩以安装螺杆轴承,或为了提升螺杆的刚性与稳定性。这类设计的滚珠丝杆称为带法兰的滚珠丝杆。由于螺杆的一端直径较大,因此带法兰的滚珠丝杆仅能从一侧安装螺帽。部分设计也会在螺杆中间使用较大的直径。这种设计中,螺杆通常交替设有右旋和左旋螺纹,并配有两个螺帽。螺杆中间最大的直径也可用于容纳支撑轴承。
生产加工的挑战
由于材料规划的考虑,通常必须将更大的公称直径选为输出变量,因此生产此类螺杆的加工工作量相当大。此外,在研磨滚珠丝杆时,法兰部分会增加制造的难度。生产成本的增加
如果生产此类螺杆的额外加工成本超过额外的材料成本,那么制造较大尺寸的螺杆通常更具经济效益。然而,使用较大尺寸的螺杆时,必须考虑螺帽的安装尺寸也需相应增加,同时必须确保可用的安装空间足够容纳更大的螺杆。套筒与环作为替代方案
为了避免采用法兰螺杆设计,可根据需求提供套筒或环作为替代方案(例如,用于扩大的轴承接触肩)。在这些情况下,稳定的接触肩可通过这些在螺纹研磨后安装的环来实现。这些组件可以松配、粘接或缩套固定。粘接支撑环的优势在于可在最终粘接前进行微调。常用的粘合剂为 Loctite 603,可在加热后轻松拆卸。为避免粘合剂进入螺帽的负载转数区域或螺帽内部,粘接过程中必须确保仅涂覆孔面而非端面。
若使用缩套支撑环,必须确保环无间隙地紧贴安装边缘,因为后续无法再调整或移动。拆卸缩套环需要较大的力,且通常无法不损坏地完成拆卸。
由于生产成本显著较高,带法兰的螺杆仅在技术上必须且无其他实用替代方案时使用。
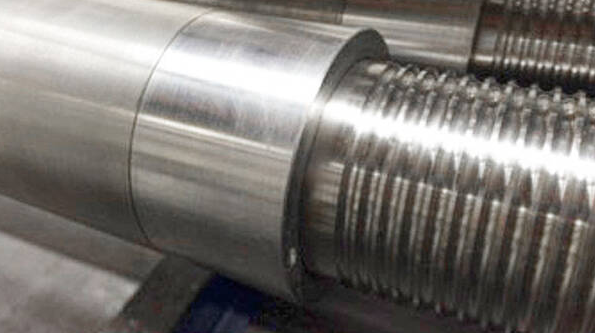
用于长达 25 米的耦合滚珠螺杆
滚珠螺杆的最大长度通常受限于原材料的供应和生产能力(如研磨、渗氮处理)。若需要更长的螺杆,可以将两根滚珠螺杆永久耦合在一起。两根经精密研磨的连接螺杆会进行对齐,使螺纹能够完全对接。这些连接螺杆负责连接两段滚珠螺杆的配合面,并采用相反的螺距方向(右旋与左旋),以进一步增强接合处的刚性。这种对齐方式透过专门设计的耦合点实现紧密配合。如果两段螺杆的行程误差几乎相同,则通常不会对质量造成显著影响。理论上,透过多个耦合点可以生产任意长度的螺杆。
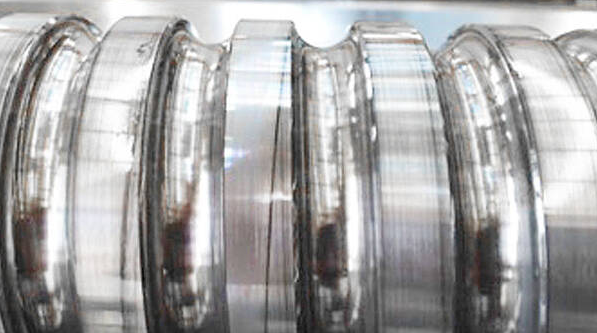
精确了解滚珠螺杆的用途及受力分布
在设计和评估耦合点时,精确了解滚珠螺杆的用途及现有的力分布非常重要。对于驱动螺帽的滚珠螺杆,耦合点通常只承受轴向力。然而,如果螺杆本身是驱动的,则除了轴向力外,还需要考虑螺杆的驱动扭矩作为负载。请向我们描述您的应用案例,我们的专家将为您提供量身定制的建议。
适用性
耦合滚珠螺杆通常只适用于水平安装。由于可能的轴向拉力及安全考虑,A.MANNESMANN 不生产垂直悬挂式的耦合滚珠螺杆。螺纹长度
滚珠螺杆的螺纹长度对于其总长度具有决定性作用。螺纹长度由有效行程、两端的螺纹结束位置以及螺帽本体的长度组成。有效行程 l_u 是螺帽可以移动的最大距离,在此距离内可保持所需的精度。其尺寸应大于结构上预计的名义行程,并且通常受端部止挡和/或限位开关的限制。螺纹结束区域 l_e 无需精度要求,因为通常不会经过此区域。而螺帽长度 l_2 可能还需要考虑防尘密封系统的安装长度。
螺杆细节
为了完全确保滚珠螺杆的功能和质量,螺杆生产过程中需要考虑各种细节,而其中一些细节无法直接与滚珠螺杆本身相关联,例如:- 轴承颈部
- 驱动组件的支撑颈部
- 螺纹结束区域
- 倒角与退刀槽
- 中心定位
- 安装螺纹
- 端部攻丝孔
- 扳手平面
- 旋转编码器接口